Helping restaurant workers report appliance problems through 86 Repairs in half the time
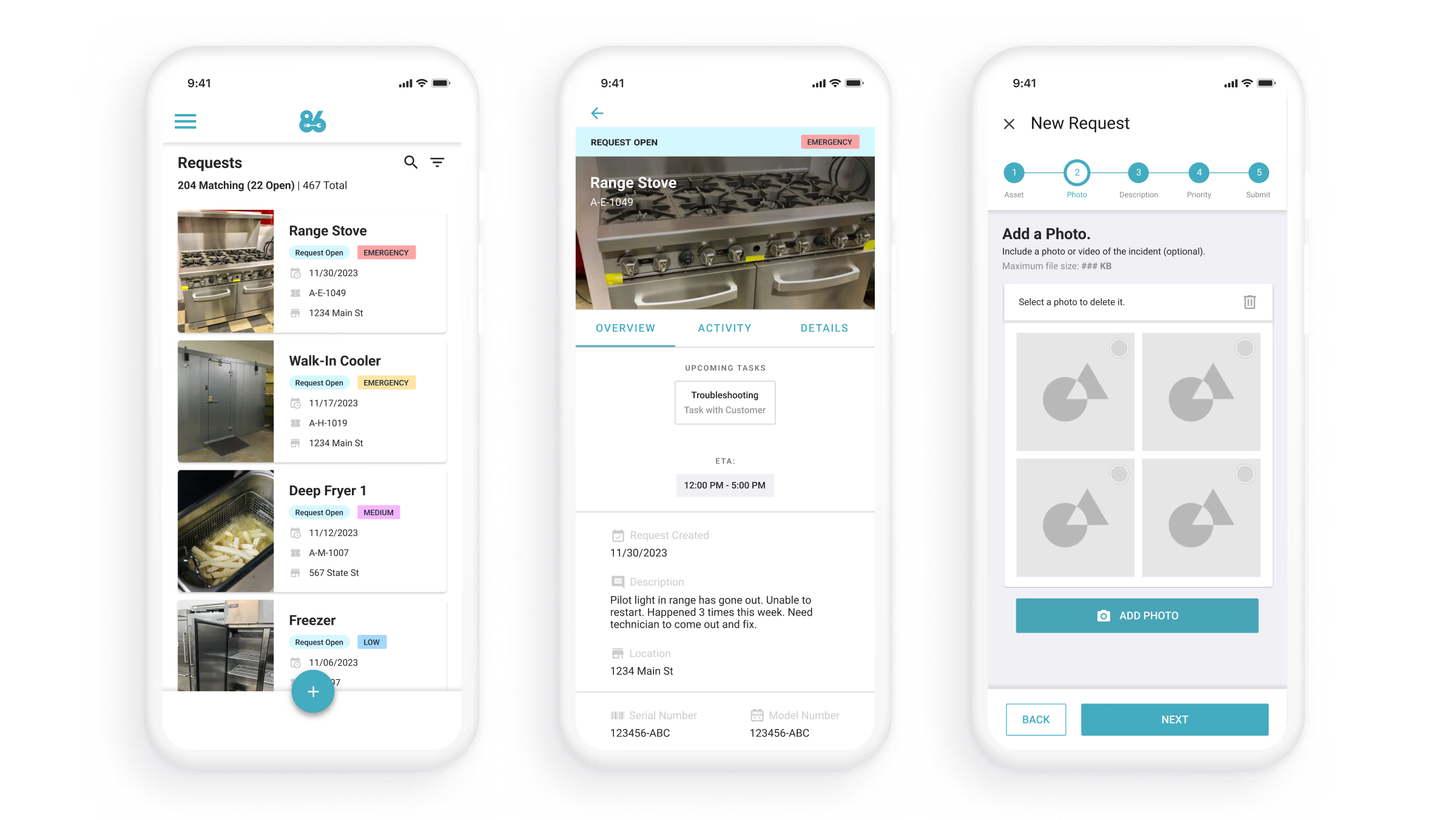

86 Repairs is a repair and maintenance solution for restaurant operators. Restaurants can use 86 Repairs’ service to contact maintenance professionals in the field or send requests to an in-house technician.
were submitted through the new mobile app within two years of its launch
every year in automated tasks, previously managed by customer service representatives
among all channels customers use to submit tickets—outperforming phone and SMS
Client Outcomes
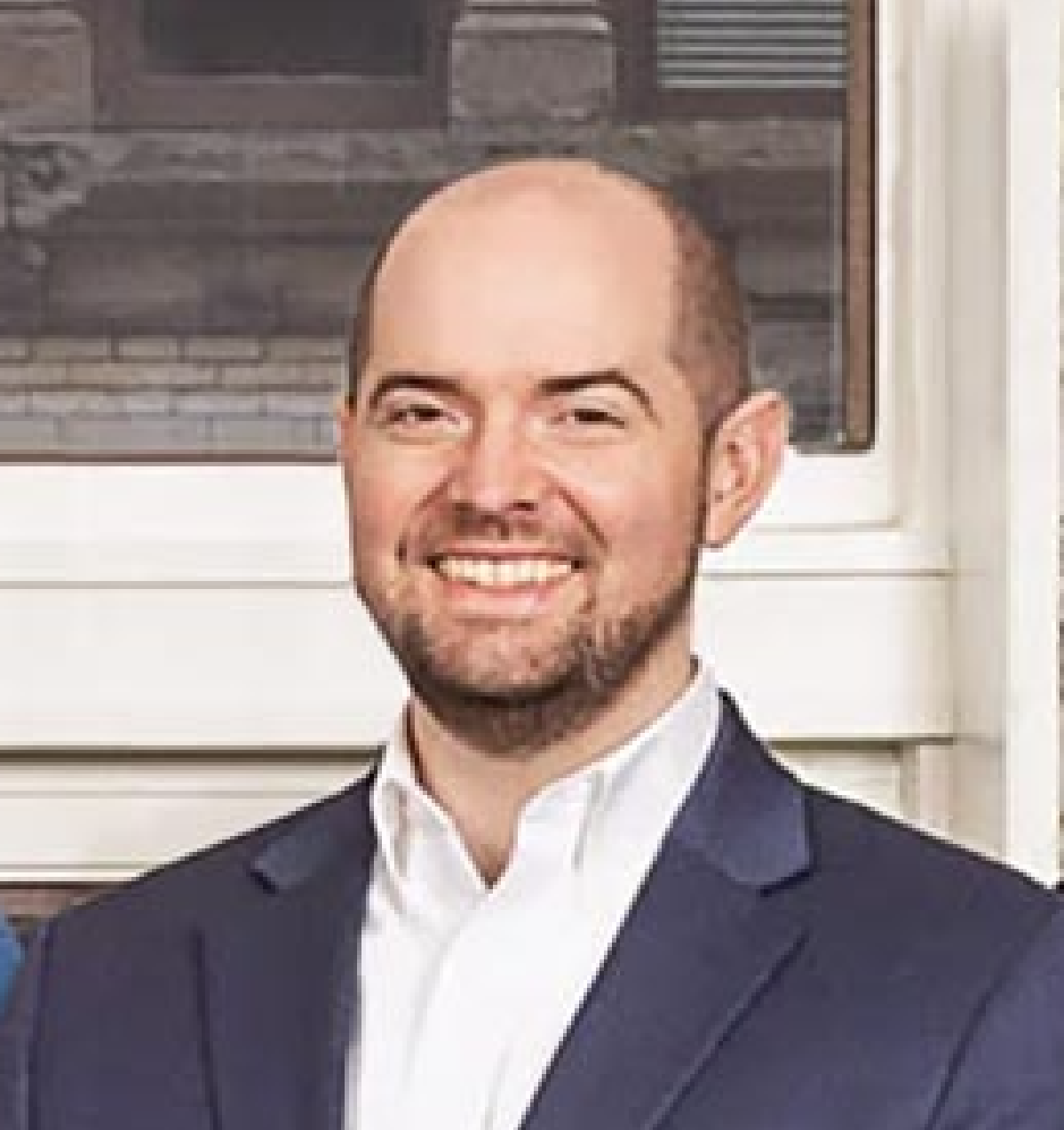
“The return on investment we got for this product—we would do it all over again and then some.”
Efficiency gains from field-tested software
Employing their field research, the Atomic team focused on presenting data more efficiently, creating a mobile interface for quicker access to crucial information. This enhancement addressed the challenge of managing large amounts of data, making it easier for users to submit tickets for repair—even in bustling kitchen environments.
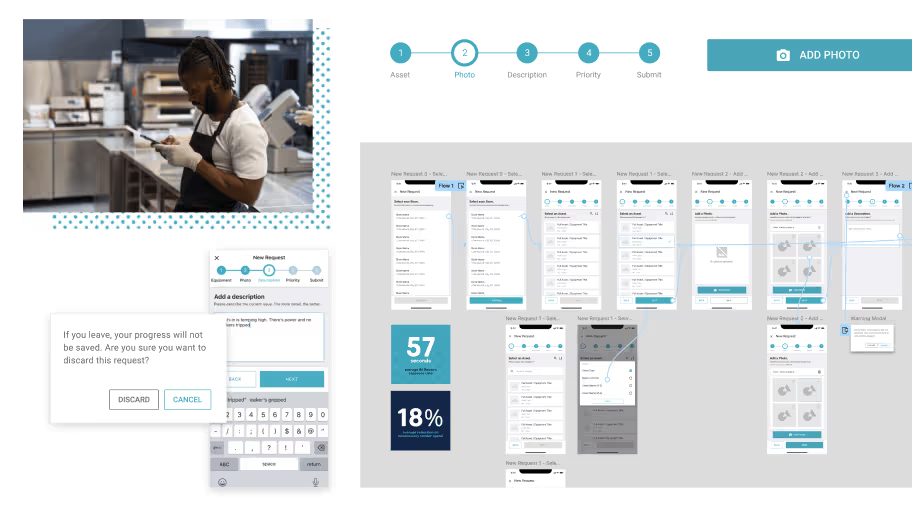
Prototype validation through field visits
During kitchen site visits in Chicago, Atomic’s multidisciplinary team began by sharing early prototypes with end-users, gathering insights, and identifying pain points. The information collected from these trips informed design choices and ensured the app met the specific needs of the end-users in their work environment.
Seamless configuration and deployment with Expo
Atomic leveraged React Native and Expo, a React Native framework, for rapid development. By using Expo, the developers could spend less time configuring and more time implementing valuable features.
Results-oriented information architecture
The mobile apps’ features focused on presenting data more efficiently, simplifying the user interface for quicker access to crucial information. This enhancement made it easier for users to submit tickets, while reducing emphasis on less important information.
Read about 86 Repairs’ Experience in their own words
See how our clients rate their experience working with Atomic on Clutch. Read verified reviews that highlight our commitment to delivering innovative solutions and exceptional results.